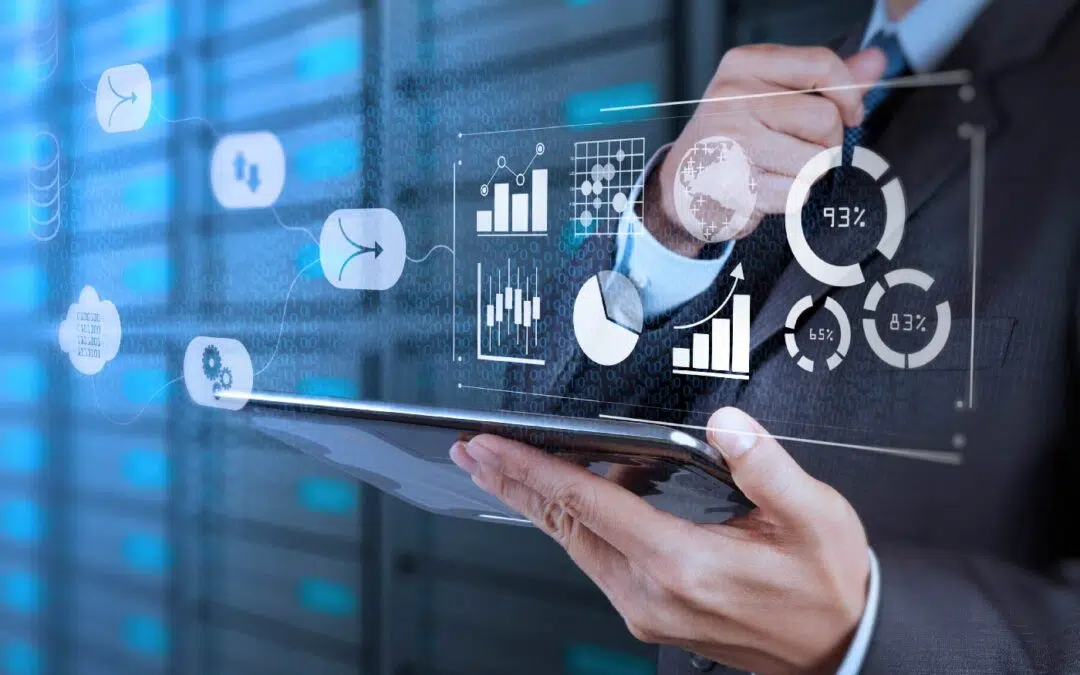
A primer on the technologies enabling Edge Analytics
The substantial rise in edge analytics applications is due to the widespread use of the internet of things (IoT), widely acknowledged by industries as the most important tech trend due to the broad range of IoT services and domain capabilities.
How does edge analytics work?
When used as a data-driven approach to extracting tangible and measurable metrics from the IoT, edge analytics enables businesses to obtain data faster by deploying advanced analytics and machine learning at the point of data collection via connected devices and real-time intelligence.
In terms of the industrial IoT industry, it is expected that industries using edge computing will grow further owing to the edge analytics advantages of dispersed aggregation and offering shop-floor data gathering across all industrial sectors.
The idea of edge analytics allows for developing an optimum model for managing data transmission from the edge and ‘smart’ data storage in data centers. Advanced analytics techniques, independent of their application area, operate behind the scenes to anticipate system component failure, keep devices operational, and ensure a continuous workflow.
Overall, edge analytics skills are actively used to develop smart machines that perform self-responsive activities and anticipate consequences.
Edge AI video-based analytics have found widespread use in a variety of areas, most notably education. Indeed, it can revolutionize the teaching-learning process by providing innovative methods for delivering instructional films in novel ways. Sony, for example, demonstrated its AI edge analytics-based solution for producing video content: its primary unit, in conjunction with different licensed appliances, demonstrates how video streaming may be elevated to a new level.
Why do edge analytics matter in 2021?
Industry 4.0 is now facing significant obstacles that are impeding its development. Computing at the edge is the answer to many of these problems. Here are some of the most significant benefits that the edge offers to Industry 4.0.
Increased interoperability
IoT systems may be a hurdle to smart manufacturing’s growth. However, an IoT network is just as good as its interoperability.Concerns about interoperability are among the most significant obstacles to its adoption since there is no standard protocol. By relocating computer operations to the edge, part of the requirement for a universal standard is eliminated. When devices can transform signals on their own, they will operate with a wider range of systems.
The edge also acts as a link between information and operational technologies.
Reduced latency
When sending data to a distant cloud data center for analysis, the latency is lengthy and unpredictable. For time-sensitive use-cases, the chance to act on the data may be lost.
Edge computing provides predictable and ultra-low latency, making it suitable for time-critical scenarios such as any use-case where the process is mission-critical or in motion. Delays in moving cars, equipment, components, people, or fluids may result in lost opportunities, excessive expenses, or security concerns.
Analytics-enabled technologies
Companies decide to include edge computing technology in their network architecture due to the number of benefits it offers. There is something for everyone, from real-time AI data analysis and improved application performance to significantly reduced operational expenses and planned downtime.
Technologies enabling Edge Analytics:
Edge Computing with Multiple Access
Multi-access Edge Computing or MEC is an architecture that allows for computing and storage resources inside a radio access network (RAN). The MEC contributes to increased network efficiency and content delivery to end-users. This device can adjust the load on the radio connection to enhance network efficiency and reduce the need for long-distance backhauling.
Internet of Things
The idea of the Cloud of Things (CoT) is still in its early stages, but it has many potentials. All computing power in a Cloud of Things is obtained from the extreme edge at the end-user.
We all have powerful gadgets in our hands, such as industrial tablets, smartphones and Internet of Things (IoT) devices in our plants. These gadgets are often underused. Although IoT devices currently have limited computing capacity, many modern devices are very powerful.
Using mobile or IoT enabled devices, cloud services may be provided directly at the edge. These devices may be coordinated to provide edge cloud services. For example, a vehicle traveling through traffic may transmit traffic warning alerts to others and re-arrange alternative routes without user involvement.
The idea of the Cloud of Things is akin to that of fog computing. All IoT devices in a CoT form a virtualized cloud infrastructure. All computing in the CoT is done by the IoT devices themselves, which are shared resources.
Fog Computing
Fog computing, fog networking, or simply “fogging” refers to dispersed computer architecture. It brings cloud computing (data centers) to the network’s edge while also locating data, storage, and applications in a logical and efficient location. This location occurs between the cloud and the data source and is often referred to as being “out in the fog.”
Future of edge analytics
Edge computing has gained traction because it provides an efficient answer to growing network issues connected to transferring massive amounts of data that today’s businesses generate and consume. It’s not simply a matter of quantity. It’s also an issue of time; applications rely on processing and responses that are becoming more time-critical.
According to projections, there will be 21.5 billion linked IoT devices globally by 2025. Consider if half of them could do computational work for other devices and services. This massive, linked computer network would be especially useful for smart manufacturing.
Conclusion
Edge analytics is a burgeoning area, with companies in the Industrial Internet of Things (IIOT) industry increasing their investments every year. Leading OEM and suppliers are actively spending in this rapidly growing industry. Edge analytics offers real business benefits by decreasing decision latency, scaling out analytics resources, addressing bandwidth problems, and cutting expenditures in industries such as retail, manufacturing, energy, and logistics.
Utthunga’s expertise in edge analytics and edge computing along with IIoT technologies enables organizations to scale their processing and analytics capabilities exponentially. Contact us for your edge analytics requirements to leverage the real-time business insights from the edge.