Why Hardware Testing Services and Hardware Pre-Compliance Testing is Required for Industries?
Performing hardware testing and compliance testing at the end of the product development cycle can be very risky due to the high cost factor. A failed hardware interoperability testing and compliance testing at the end of product development cycle will require reserving time in the lab along with re-designing your device. Pre-compliance testing is an affordable method to ensure that your device passes the final product certification testing flawlessly.
Proper attention to hardware testing can offer a number of benefits such as
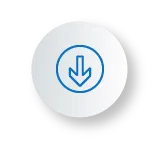
Lower Risk of Field Failure
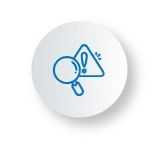
Early Detection of Errors and Fixing of Potential Issues
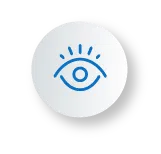
Enhanced Visibility into the Product Development Process
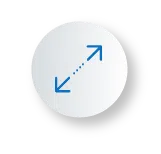
Increased Scalability
Enhanced Safety
Increased Savings
Reduced Issues Related to Warranty
Embedded Hardware Testing Services Provided by Utthunga
Utthunga’s embedded testing team with highly experienced test engineers have successfully executed projects by efficiently adapting to the diverse functional knowledge and test setups. We offer expert verification and validation services throughout the product lifecycle, from designing, development to testing, production support, and post product support across multiple domains as well as technologies.
Our embedded hardware testing services include
Hardware
- Board verification and validation (as per IPC Standard)
- Unit, integration and module testing
- Electrical testing
- Thermal, power and signal integrity
- Signal analysis
- I/O boundary conditions testing
- Intrinsic safety & safety verification (SILx)
- Security
Firmware
- Unit, integration and module V&V (coding standards, functionality)
- System level testing/end-to-end testing
- FOTA
- Resource utilization
Compliance / Calibration / Certification
- RoHS
- REACH
- Environmental, operational parameters
- IS, Safety, EMI / EMC
- Protocol compliance – HART, EtherNet/IP, OPC
- Type, Routine, Acceptance, Calibration from accredited agencies
Protocols
- CTT (Compliance Test Tool)
- Pre-compliance
System
- Functional tests
- Interoperability testing
- Accessibility
- Security
Why Utthunga for Embedded V&V Services?
Verification and validation testing is primarily concerned with answering two main questions: “Are we building the product right?” and “Are we building the right product?” Utthunga can provide the answers to these questions.
Verification answers the question, “Are we building the product right?” and checks if all the specifications (requirement, design, implementation, testing, maintenance and support) are correctly implemented in the system.
Validation answers the question, “Are we building the right product?” and checks that the user’s needs and all the stakeholder’s goals will be met. It makes sure that you are not building a product based on faulty assumptions and ignorance.
We are a leading provider of verification and validation services. Our rich experience in different embedded platforms and operating systems help us to enable you to deliver excellent products to your customers.
We provide embedded V&V services that include but not limited to
- Hardware (system and application) integration testing
- Security testing
- Production test jig design and development
- Certification and pre- compliance testing: HART, CE, FCG, IS , SIL
- MQTT/CoAP/M2M cloud and device integration testing
- Product certification and support: EMI/EMC, CE and IS Certification (ATEX/IECEx)
- Adherence to industry standards like IEC 60079-15, FM 3611, CSA C22.2 #213, ATEX, IP65/IEC 60529 and others
- Adherence to EMI/EMC, Environmental Standards: Conducted Emissions , Radiated Emissions, Electrostatic Discharge Immunity, RF Radiated Immunity, Electrical Fast Transients / Burst Immunity, Power Frequency Magnetic Field Immunity and more
Our Strengths
- Experienced embedded systems resource pool
- State of the art lab facility
- Flexible engagement models and customization as per requirement
- Interoperability and pre-compliance test center
- PROFIBUS and PROFINET Competence Centre (PI)
- 13+ years of experience industrial domain
- Member of key industrial consortiums like the OPC Foundation, FDT Group, FieldComm Group (FCG)
- Accredited FDT Test and Certification Centre
FAQs
1. What is product pre-compliance testing?
Product pre-compliance testing is a cost-effective low-risk method to ensure your product under test will pass the final compliance testing.
2. What will be the role of hardware integration testing in Industry 4.0?
Industry 4.0 is an amalgamation of diverse IoT systems and embedded devices. Hardware product interoperability testing ensures that these heterogeneous systems can communicate and work seamless with each other. Interoperability is key to ensure that the analog data generated in the lowest level of the plant (sensors and field devices) makes its way through to other layers, else data silos or lost data is the antithesis of Industry 4.0.
3. What are the various product testing methods for industrial hardware products?
There are a number of methods to test the different parts or sub-assemblies of a product. Some of these include environmental testing, automated testing, and regression testing among others. These test methods include power quality, power usage, run-up time, pull-in current, voltages, etc.
4. What are the methods you use in product testing?
Our product testing involves various methods like testing with a simulator, sequencing through different test steps, measurement of various physical properties, and analyzing the acquired test data.