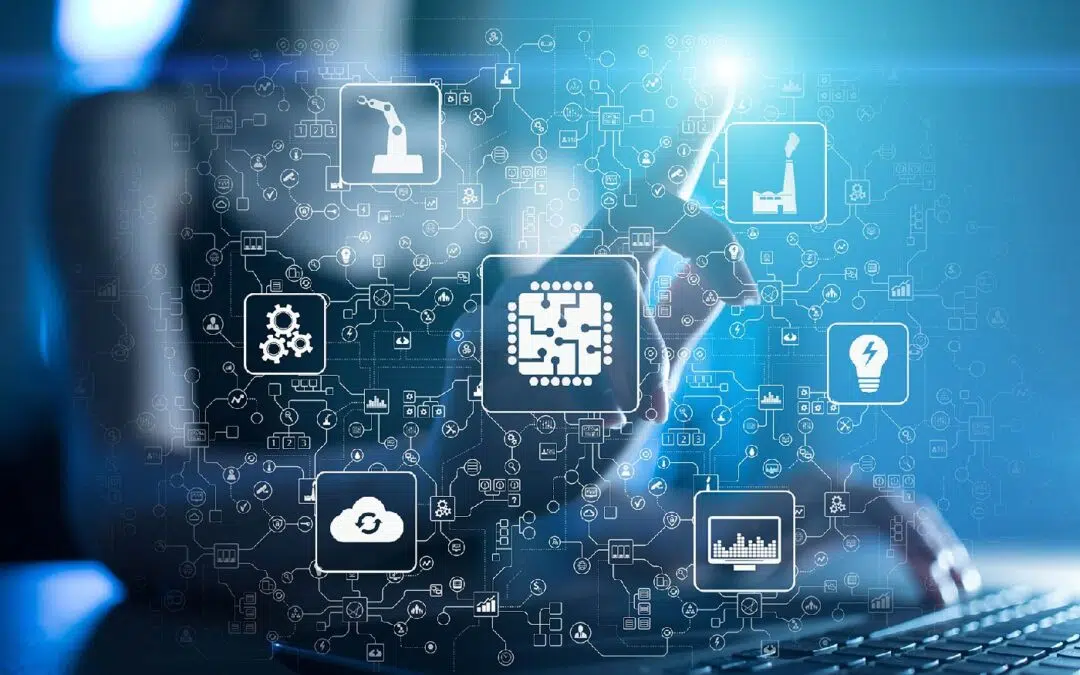
9 Technologies Which Form the Building Blocks for Industry 4.0
The rise of Industry 4.0, the new digital industrial technology
Today the manufacturing scene in India mainly comprises of small and mid-end capital good industries, textile, pharmaceuticals, leather, and auto manufacturing. Over the past few decades, these industries have moved toward industry 3.0 to improve the efficiency of their manufacturing process with the help of automation and robotics.
Following suit with American and European companies, Indian manufacturers are now leapfrogging into Industry 4.0 with the aim to automate decision making across enterprises through efficient data analytics that can help improve quality and reduce human errors.
The major building blocks of Industry 4.0 that help to eliminate the drawbacks of Industry 2.0’s low-cost labour and ineffective management include: cloud computing, cybersecurity, Augmented Reality, Big Data analytics, Industrial Internet of Things, Additive Manufacturing and more.
Let’s take a brief look at the nine Industry 4.0 digitalization trends and technologies that can tremendously improve the profitability margin of your organization by bringing together isolated cells into an integrated, optimized and automated workflow.
Top 9 technologies that drive Industry 4.0
1. Autonomous Robots: Flexible and co-operative, these are the key qualities used to describe autonomous robots. Taking advantage of advanced robots has proven to be highly effective in improving the quality and cost-effectiveness of the manufacturing process. Successors to assembly lines and mechanical arms, today’s autonomous robots are being leveraged by industries around the world for their ability to work together with humans and machines through learning and interaction.
2. Simulation: Simulation technology helps to create virtual clones of real-world machines, products, and humans. The main advantage of simulators in the product development, material development and production processes is that it allows you to first test and optimize the machine settings for a product in the virtual world before deployment. This way simulation can help to reduce failures in any of the production processes, ensure quality and also dial down the setup times for the actual machining process. 3D Simulation is majorly used in plant operations where it is highly important to make the best use of real-time data to create the next best product. With continuous and rapid testing of the 3D model, high-quality physical products can be created and deployed in the market on time.
3. Horizontal and Vertical System Integration: With horizontal and vertical system integration, a company can enable cohesiveness and cross-functionality among its various departments and functions.
- Horizontal integration: Enables networking and exchange of product and production data between multiple stakeholders, individual machines, or production units.
- Vertical integration: Provides control over the supply chain system through integration.
4. Industrial Internet of Things: IIoT deals with connectivity for machines, smart factories, and for streamlining operations. IIoT connects critical machines and precise sensors including location-aware technologies in high-take industries and generates a massive volume of data. The communication-based eco-system for the industrial sector (manufacturing, supply chain monitoring, and management systems) brings users, analytics and smart machines together to simplify the collection, analysis, exchange, and monitoring of actionable data.
5. Cybersecurity: As Industry 4.0 technologies require increased connectivity, it is highly crucial to protect critical industrial systems and manufacturing lines from cyber-attacks. Businesses make use of cybersecurity to protect their networks, systems, and data from cybersecurity threats.
6. Cloud: With Industry 3.0 propelling production, there will be an increase in data sharing across different verticals and sites within the company. With Cloud, you can store and access data and programs over the internet. By deploying machine data and functionality through cloud technologies that are part of Industry 4.0, you can now make on-time data-driven decisions by coordinating with internal as well as external stakeholders.
7. Additive Manufacturing: Popularly known as 3-D printing, additive manufacturing is used by companies to create prototypes of individual product components. This technology is being widely used by industries to create customized products that offer various production and cost advantages.
8. Augmented Reality: With augmented-reality glasses, eye-pieces, mobile-devices and other products you can provide users with real-time data that can facilitate decision making and improve their work output. AR technology enables access to the right information at the right time and empowers each user to work and make decisions individually.
9. Big Data Analytics: This is perhaps one of the most important building blocks of Industry 4.0. Big Data Analytics enables the collection and also the comprehensive evaluation of data from different sources. With data analysis, you can quickly and easily identify patterns, correlations, and trends that can significantly reduce product failures and also optimize the creation of better quality products. With Big Data Analytics, you can discover and examine large and varied sets of data procured from production equipment and systems and also enterprise- and customer-management systems to support real-time and informed decision-making that will be critical for your business.
How can Utthunga transform your business with Industry 4.0?
Are you looking to fast-track and improve the efficiency of your manufacturing process with Industry 4.0 technologies? At Utthunga, we help you transition into a smart-factory by streamlining and unifying several and disparate manufacturing processes. With our automation portfolio, we can help you to:
- Digitalize industry hardware to make field devices smart.
- Connect field devices and other industrial assets with our IIoT platform called Javelin that can generate rich visualization and analytics.
- Set protocols for getting data for different assets (OPC, FDP).
- Follow the industry standards to build business applications.
These services can help to:
- Reduce the time taken to collect and analyze data derived from business systems.
- Reduce errors that happen due to manual handling of data.
- Receive accurate and timely-data on machine performance.
- Diagnose problems quickly and rectify issues during planned the down-time for maintenance.
- Provides greater visibility of plant and floor equipment.
- Make informed decisions regarding asset utilization.
- Conduct environment-based and condition-based monitoring to measure performance.
Our Industry 4.0 solutions also simplify interactions between suppliers, producers, and customers as well as human and machines. To know more about how we can help your business benefit from Industry 4.0 technologies, visit https://utthunga.com. Just drop a mail at [email protected] or call us at +91 80-68151900 to know more in detail about the services we offer.