Introduction
Why Field Device Testing is Required For Industries?
Field devices support various protocols and standards for easy adoption and interoperability. A field device OEM should also solicit pre-certification testing to ensure its field devices meet the protocol specifications such that their products can be certified by the concerned standards organization (like OPC Foundation, ODVA, ETG, PI, etc.)
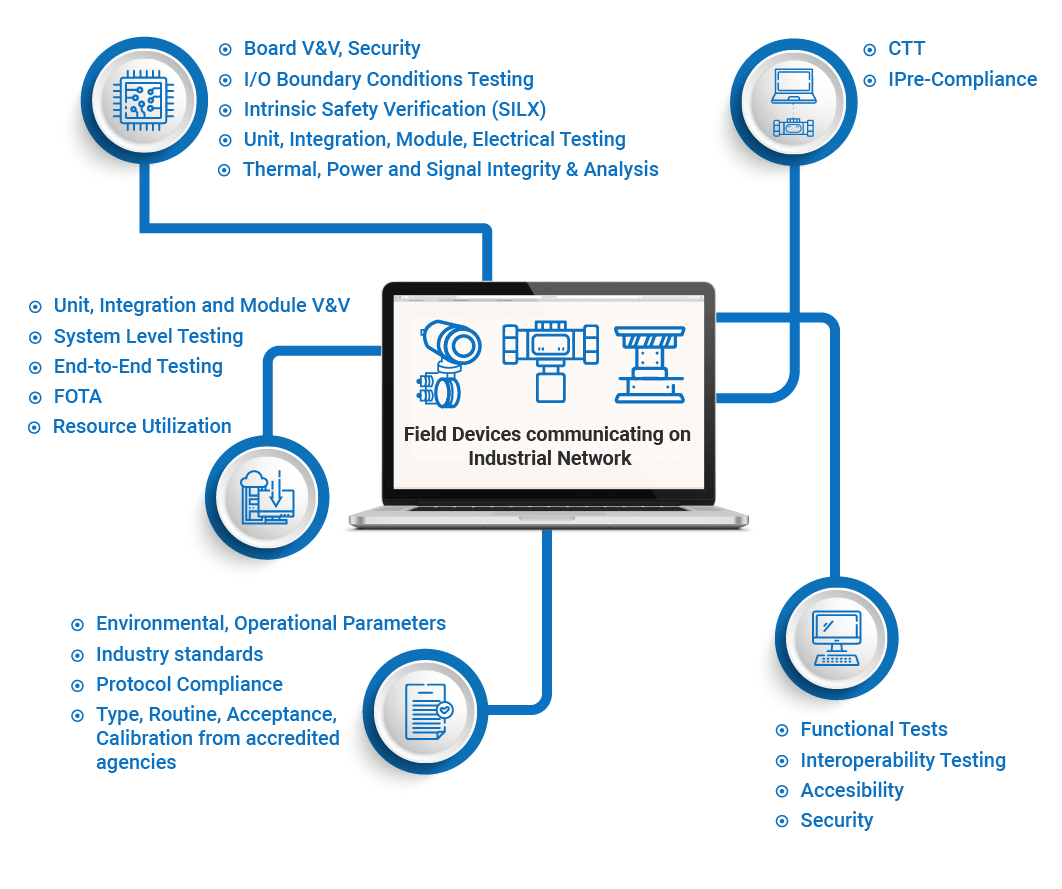
Device Testing Services Provided By Utthunga
At Utthunga, we offer cutting-edge device testing services in both hardware and firmware areas. Our device testing team of highly skilled test engineers have executed complex projects by quickly designing and creating efficient test setups, adapting to existing setups and functional knowledge.
We provide end-to-end testing service with flexible engagement models with our deep understanding of industrial automation and certification capabilities. We are also a protocol compliance testing company and some of the features of our testing services include:
- User-friendly automation framework for easier maintenance and reliable results
- Support for various test automation tools like Ranorex, etc.
- Functional, system and integration testing of the devices and configuration tools
- Interoperability testing with different scanner devices
- Design and development of test jig and verification on the test jig
- Pre compliance testing of the devices and experience in fixing any non- compliance issues
Hardware Testing
- In-depth signal analysis, voltage level, frequency, rise time fall time characteristics, noise levels etc.
- Board level testing and validation
- Power block testing and analysis
- Electrical testing and validation
- Safety and security standard measures (silx)
- Unit/module functionality testing
- Sensors, wireless devices, displays, various data acquisition units and gateways etc.
- Integration testing: h/w unit level and system level (top to bottom/ bottom to top/ hybrid incremental approach)
- Pre compliance – physical layer testing (for HART devices)
- Acceptance testing
Firmware and System Testing
- Unit/module code and quality analysis
- Coding and project guidelines checks (Ex. MISRA)
- System-level end-to-end testing
- Stability, durability, availability, scalability, reliability, recovery and remote monitoring with diagnostics tests
- Pre-compliance tests
DLL, UAL, CAL testing using HART 192 Test Kit and device-specific commands testing (for HART devices)
Compliance and Certification Support for CE, FCC, UL, ATEX, etc.
- Class & Directive identification
- Applicable test cases
- Pre-compliance testing
- Technical documents preparation
- Sample submissions
- Declarations
- Affixing marks
Why Choose Utthunga For Field Device Testing?
- End-to-end device testing including hardware, firmware and configuration software
- Reduced execution time with exhaustive test coverage of all scenarios for each device
- Successful automation of manual test cases
- Experienced engineers who can provide you consultation service for troubleshooting your certification-related issues
- As a protocol compliance testing company we provide feasibility study of implementing new communication protocols on existing devices
- Integration testing of the communication drivers with other industrial automation standards like FDT, FDI, OPC, etc.
- As an FDT Accredited Test & Certification Centre, we can help you in certifying your DTM for FDT specification conformance
FAQs
1. Does Utthunga provide Pre-Certification Testing?
Yes, we provide a wide range of verification and validation services including pre-certification testing for industries.
2. How do field instruments work, and what kind of calibration do they require?
- Transducer calibration which focuses on the transducer input-output output relationship
- Physical end-to-end calibration
- Data system calibration which simulates or models the input of the entire measurement system
All these calibrations ensure that your device measurements are accurate which will positively affect your production process because all the measurements will be correct. This also reduces the variation with respect to the technical specification as well as help in preventive maintenance.