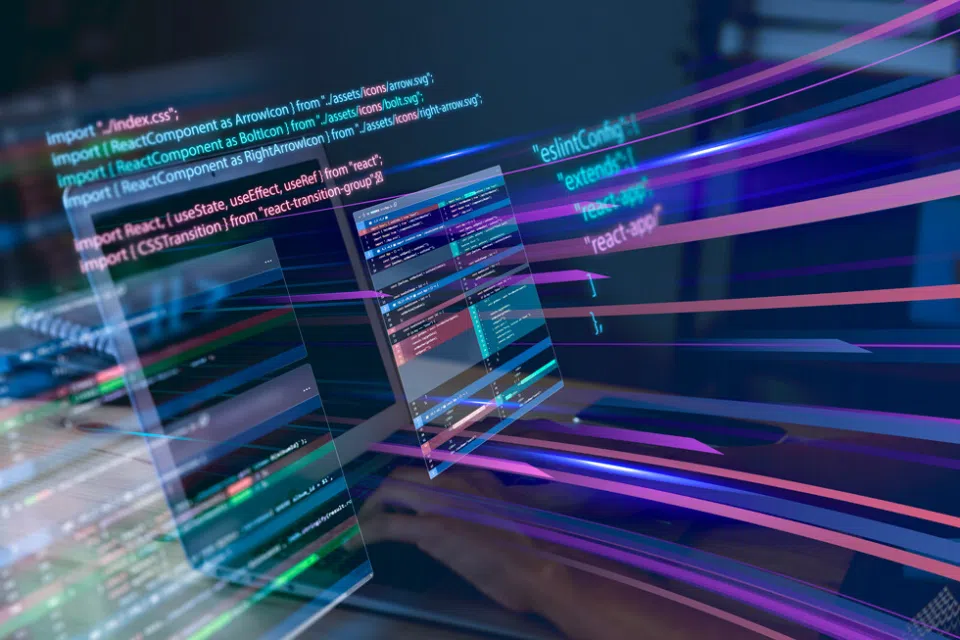
The Benefits of Rapid Application Development for Your Business: A Comprehensive Guide
Staying competitive today takes more than just good ideas—it takes agility and efficiency. That’s why many businesses are turning to Rapid Application Development (RAD) methodologies. RAD helps teams develop and deploy applications quickly, leading to faster time-to-market and greater customer satisfaction. It’s a smarter, faster way to build software, with an emphasis on quick iterations, continuous feedback, and real collaboration between developers and end users.
In this guide, we’ll walk through the key benefits of Rapid Application Development for your business, from faster delivery and better flexibility to cost savings and improved quality.
Key Benefits of Rapid Application Development
Faster Development and Deployment: RAD emphasizes iterative development cycles and quick prototyping, allowing businesses to deliver applications faster compared to traditional development methods. This speed enables businesses to respond swiftly to market demands, gain a competitive edge, and seize new opportunities.
Cost-effectiveness: RAD minimizes development costs by streamlining the software development process. With its focus on iterative development, RAD reduces the time and effort involved in extensive upfront planning. Additionally, rapid application development promotes collaboration between developers and end-users, which ensures that the final product meets customer requirements and reduces costly rework.
Better Collaboration: RAD encourages close collaboration between developers, end-users, and stakeholders throughout the development process. By involving end-users early on, rapid application development enables developers to gather feedback, incorporate changes, and address issues promptly. This collaborative approach enhances the accuracy of requirement gathering, reduces misunderstandings, and increases overall customer satisfaction.
Improved Quality: Through the iterative development process, RAD facilitates continuous testing and feedback, leading to improved quality and reduced defects. Early and regular user involvement ensures that the application meets user expectations, resulting in higher customer satisfaction. By incorporating feedback and making necessary adjustments promptly, RAD helps identify and rectify issues early in the development cycle.
Why Rapid Application Development Matters for Your Business
Rapid Application Development isn’t just about speed, it’s about building better software with less friction. It enables businesses to respond faster, collaborate more effectively, and deliver solutions that actually meet user needs.
At Utthunga, we bring this approach to life. With years of experience and deep technical know-how, we help businesses build scalable, flexible, and secure applications using RAD principles.
If you’re looking to accelerate development without losing control or quality, let’s talk.
Contact Utthunga to learn how Rapid Application Development can work for you.