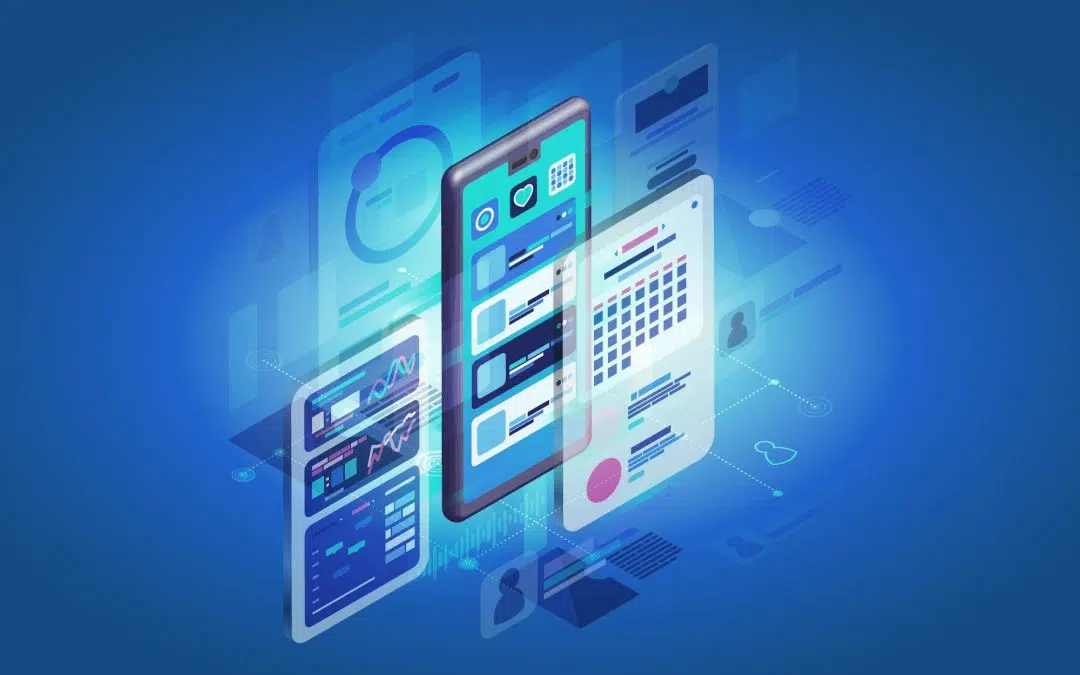
Revolutionize OT App Development with Utthunga’s Mobile App Copilot
Imagine the scene in a modern manufacturing plant: a seasoned engineer, armed with a tablet/mobile in hand, weaving through rows of machinery to commission a new production line. With each passing moment, the pressure mounts as he grapples with a slew of software tools, juggling compatibility issues, deciphering complex protocols, and navigating clunky interfaces.
This struggle is all too familiar across industries worldwide, from manufacturing to energy production, where professionals face the daunting task of keeping operations running smoothly amidst the ever-evolving landscape of technology. But what if there were a guiding light — a tool to simplify this intricate journey?
Introducing Mobile App Copilot, a revolutionary tool in Product Engineering design, which is developed based on a proven technology used to build 50+ mobile applications on different platforms such as Android, IOS, and Windows. Unlike any other tool, it’s an innovation that simplifies app development for both technical and non-technical users. It’s a game-changer designed to transform the development of Operational Technology (OT) applications for mobile devices.
Envision a world where creating OT applications is no longer a challenge but a streamlined process. With the Mobile App Copilot, this becomes a reality. By automating the creation of OT tools that support multiple requirements simultaneously, it empowers engineers to easily develop adaptable apps across various platforms and protocols.
The Sample Use Cases:
1. Streamlining Field Device Diagnostics for OEMs/ISVs/MSME
Problem Statement:
In the realm of industrial machinery, ensuring the health and performance of field devices is paramount for operational efficiency. However, when service engineers/supervisors encounter issues with field device health, accessing the necessary tools for diagnostics can often be a cumbersome and time-consuming process. Traditional methods of generating mobile apps for field device diagnostics often involve lengthy development cycles and delays, leading to prolonged downtime and decreased productivity.
Solution:
With Mobile App Copilot installed and accessible to the admin or technical support team at the OEMs/ISVs/MSME, the process of creating a mobile tool for field device diagnostics becomes seamless and efficient.
When a service engineer submits a request for a mobile tool to connect to field devices and perform health and diagnostics checks, the admin or technical support team can leverage the capabilities of the Mobile App Copilot to swiftly develop and enhance a mobile app tailored to the specific needs of the service engineer.
By defining variables, communication structures, and user interfaces, Mobile App Copilot automates the creation of a mobile application that supports multiple industrial standard protocols and mediums, ensuring compatibility with a wide range of field devices.
2. Empowering End Customers with Scalable Mobile App Solutions
Problem Statement:
For end customers in industrial settings, keeping pace with evolving technology and expanding device compatibility can be a challenge. When faced with the need to support more devices, they often encounter the dilemma of either developing a new mobile app or modifying the existing one, both of which can be time-consuming and costly endeavors. Additionally, reliance on technical expertise for app development further complicates the process.
The Solution:
Utthunga’s development team leverages Mobile App Copilot to create a mobile app solution that supports packages on the fly.
When an end customer requests support for additional devices, our development team springs into action. Leveraging the capabilities of Mobile App Copilot, they develop and package the required functionalities to seamlessly integrate with the existing mobile app.
The Mobile App Copilot is designed to consume runtime packages, allowing for dynamic integration of new device support without the need to modify the app itself. This ensures that the end customer can easily access the latest functionalities without any disruptions to their workflow.
The Benefits of Mobile App Copilot
- Streamlined Development:
With its low-code, no-code interfaces, Mobile App Copilot accelerates development, reducing time-to-market and allowing teams to focus on innovation rather than coding. - Cross-Device Compatibility:
Mobile App Copilot supports multiple platforms, protocols, and mediums, ensuring seamless integration across devices and environments. - Versatility:
From commissioning to diagnostics, Mobile App Copilot adapts to a wide range of industrial applications, providing a versatile solution for diverse needs. - Ease of Use:
Intuitive interfaces make Mobile App Copilot accessible to both technical and non-technical users, empowering teams to collaborate effectively. - Efficiency:
By automating repetitive tasks and streamlining processes, Mobile App Copilot boosts efficiency, allowing engineers to focus on high-value activities. - Scalability:
Whether deploying a single app or managing a fleet of devices, Mobile App Copilot scales effortlessly to meet the demands of any project. - Cost-Effectiveness:
By reducing development time and minimizing the need for custom coding, Mobile App Copilot offers a cost-effective solution for OT application development. - Mobile App Creation On-The-Go:
With Mobile App Copilot, engineers can create and deploy apps from anywhere, ensuring flexibility and responsiveness in today’s fast-paced industrial environments.
The Conclusion:
Mobile App Copilot isn’t just a tool—it’s a catalyst for innovation, empowering industrial professionals to navigate the complexities of app development with confidence and ease. From concept to execution, Mobile App Copilot provides an end-to-end solution for On-The-Go App generation, revolutionizing the way we approach mobile OT applications in the industrial sector.